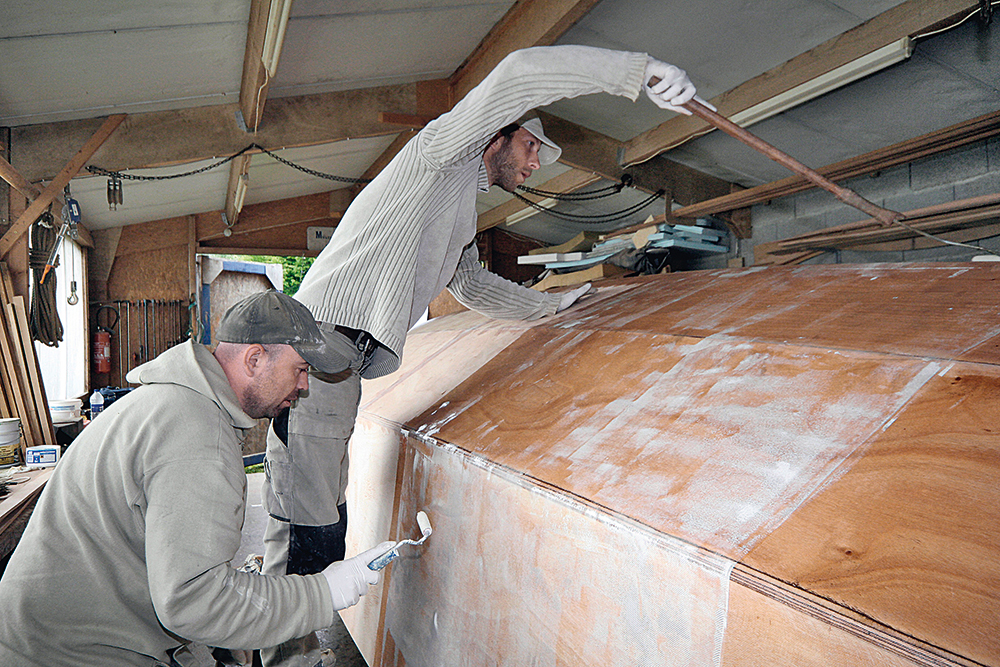
Par Jean-Yves Poirier – Associer des fibres synthétiques au bois permet d’obtenir un matériau plus résistant aux chocs et bien plus facile à entretenir. Au prix de quelques précautions simples, les techniques de stratification sont accessibles à tous.
La trace laissée par un objet métallique lourd tombant sur un pont en contre-plaqué suffit pour se convaincre que le bois supporte mal les chocs localisés ! Mais si l’on recouvre cette surface avec une ou plusieurs couches de tissu de verre, sa résistance au poinçonnement, son étanchéité et sa longévité augmentent considérablement. Pour ce faire, les résines époxy sont les seules à donner des résultats fiables à long terme, les polyesters présentant des qualités d’adhésion, de souplesse et d’étanchéité notoirement insuffisantes. Très en vogue jusqu’aux années soixante-dix, en partie car elles étaient peu coûteuses, les stratifications polyester ont tué bien plus de bateaux qu’elles n’en ont sauvé !
Au final, un panneau en bois stratifié supportera les agressions du milieu marin aussi bien sinon mieux que le polyester conventionnel, légèreté et résistance à la fatigue en plus. Cerise sur le gâteau, l’esthétique du bois verni peut être conservée car une stratification est parfaitement transparente, si l’on dépose moins de 300 grammes de verre par mètre carré. Ce procédé permet également de développer des techniques de fabrication nouvelles, comme des bouchains composites ou des joints-congés structuraux (CM 212). Il aide aussi aux finitions, un revêtement – relativement – épais masquant les imperfections du support.
La pratique aidant, chaque opérateur tend à développer ses propres habitudes de mise en œuvre, mais elles suivent peu ou prou les règles ci-dessous. Dans tous les cas, la réussite d’une stratification est liée au soin mis à la préparation des différents outils – bacs et rouleaux en quantité suffisante –, de la résine et du durcisseur – en respectant les conditions de température (18° C minimum) et d’hygrométrie (moins de 80 %) –, des pièces de tissu prédécoupées et numérotées.
Avant d’entreprendre un travail d’envergure, les débutants auront intérêt à s’entraîner d’abord sur de petites surfaces.
La pose “humide” plus contraignante que la pose “sèche”
La première opération consiste à soigneusement mastiquer et poncer les défauts de surface, puis à dégraisser et dépoussiérer la coque. Deux méthodes peuvent alors être mises en œuvre pour stratifier. Celle dite “humide” consiste à déposer une couche de résine/durcisseur sur le bordé avant d’y appliquer le tissu. Si cette technique facilite la pose sur des surfaces verticales ou en aplomb, elle présente l’inconvénient de rendre très difficile, voire impossible, une modification ultérieure de la position du renfort.
À l’inverse, la méthode “sèche” consiste à appliquer le tissu sur une surface dépourvue de résine, puis à verser et répartir cette dernière par-dessus le tissu avant d’imprégner progressivement le support.
Cette technique est nettement plus sûre que la précédente car on peut corriger le drapage (positionnement du tissu sur la coque) très facilement et à tout moment. Pour commencer, on prépare les laizes en les numérotant et en repérant leur emplacement sur la pièce à stratifier. Puis on déroule délicatement le tissu en suivant les repères. Une pose longitudinale offre l’avantage de présenter moins de découpes et donc une meilleure continuité du renfort, mais un drapage transversal, plus simple de mise en œuvre, est également envisageable. On lisse la surface à la main ou, mieux, avec une brosse souple pour éliminer les bulles et les plis. À l’aide d’un rouleau ou d’une raclette souple – préférable au premier outil qui tend à entraîner le tissu avec lui –, on fait pénétrer la résine à travers les fibres du tissu, qui deviennent progressivement transparentes. La répartition doit être aussi homogène que possible.
En principe, un tissu correctement imprégné à la main absorbe environ 1,2 fois son poids en résine et présente un aspect mat et texturé sur toute sa surface. L’entraînement permet d’éviter les surplus de résine, visibles à leur brillance. Étrave et sole peuvent recevoir deux ou trois plis de tissu supplémentaires pour mieux résister à l’échouage.
Enfin, deux ou trois couches de résine de finition permettent de remplir la trame et de protéger les fibres de l’usure.
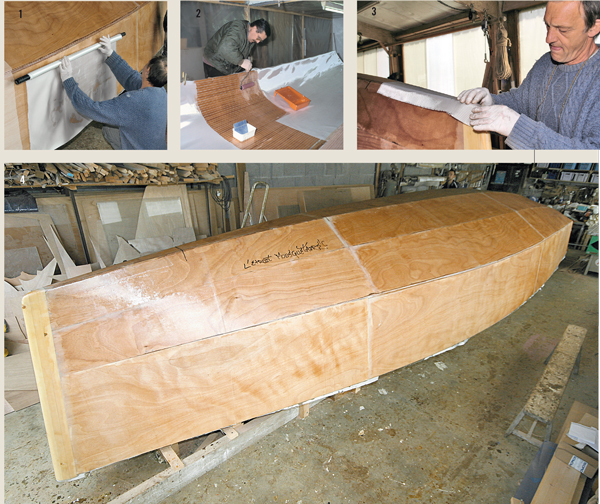