
Par Jean-Yves Poirier – Popularisée dans les années soixante, la construction cousue-collée est sans doute la technique la plus simple et la plus rapide qui soit. Contrairement à la rumeur, elle n’est nullement réservée aux petites unités.
1/ Panneaux et couture
L’idée d’assembler les bordages à l’aide de liens n’est pas franchement nouvelle. Il y a près de cinq siècles, de nombreuses pirogues polynésiennes ont été construites ainsi, tout comme le navire funéraire de la pyramide de Gizeh. Mais c’est au tout début des années 1960 que la technique du cousu-collé telle que nous la connaissons aujourd’hui a été mise au point. Son initiateur est le Britannique Ken Littledyke, un professeur de menuiserie qui fabriquait ses canoës en cousant des panneaux de contre-plaqué avec du fil à pêche avant de les solidariser à l’aide de bandes de tissu de verre et de résine polyester.
Séduit par cette méthode originale, Barry Bucknell, un présentateur de télévision spécialisé dans les émissions de bricolage, s’associe en 1962 avec l’architecte naval Jack Holt pour concevoir un petit dériveur de 3 m de long que chacun pourra construire à moindre frais dans son garage. Le Mirror, qui porte le nom du quotidien qui l’a parrainé, va connaître un succès fulgurant, la série comptant aujourd’hui plus de soixante-dix mille exemplaires !
Près d’un demi-siècle plus tard, les matériaux ont évolué et l’époxy a remplacé le polyester, mais les grands principes de cette technique simple et économe restent les mêmes. Quelques gabarits temporaires suffisent, la construction ne nécessitant ni tracé en grandeur, ni mannequin, ni chantier. La structure étant entièrement collée, la visserie est limitée au strict minimum. Les ajustages tolèrent un niveau d’imprécision assez élevé, ce qui facilite le travail du néophyte. La structure intérieure est largement simplifiée, les emménagements participant à la rigidité de l’ensemble… Pourtant, malgré tous ces attraits, le cousu-collé peine à trouver sa voie en dehors du cercle des petites unités. Rien ne s’oppose pourtant à la mise en œuvre de bateaux plus importants, comme l’ont démontré le chantier américain Devlin Boat ou le français Olbia. On se gardera toutefois d’aller au-delà de 12 m de long, car la manutention des panneaux – obligatoirement d’un seul tenant – et la mise en place des renforts nécessaires finissent par annuler les avantages de la formule.
Un assemblage par fil de cuivre ou colliers
Le cousu-collé n’emploie qu’un minimum de matériau : du contre-plaqué et de l’époxy, système adhésif performant qui permet de résoudre tous les problèmes d’assemblage, de stratification et de finition. Légère, rigide et homogène, la structure finale est obtenue en un temps record. L’outillage nécessaire est également limité et le matériel lourd superflu.
Comme le volume final est défini par le seul périmètre des panneaux, l’architecte doit veiller à leur caractère développable, pour éviter creux, bosses ou vrillage. Une maquette à échelle réduite peut y aider, mais une modélisation informatique (CM 228) offrira les meilleures garanties de résultat, surtout si on l’associe à une découpe numérique (CM 192). Enfin, si les coques cousues-collées sont toujours à bouchains vifs, rien n’empêche de multiplier ces derniers ou de ployer le contre-plaqué pour se rapprocher des coques en forme.
Toutes les expériences sont possibles en matière de cousu-collé, mais elles ne s’éloigneront guère du processus illustré ici par la construction d’un kayak de mer de 5 m de long. Le volume de la coque est obtenu par l’assemblage du périmètre de chaque panneau de bordé.
En cas de travail à partir d’un tableau de cotes manuel, le constructeur doit veiller à tracer des courbes précises et surtout symétriques sur chaque bord, faute de quoi la coque risque de se vriller ou de se déformer dans le sens de la longueur. La fabrication commence par l’assemblage des panneaux de bordé par doublante ou scarf (CM 214). On reporte ensuite les cotes qui serviront à tracer les périmètres, une opération qui nécessite d’opérer sur une surface plane et non en équilibre sur deux tréteaux – surtout si le contre-plaqué est mince – pour garantir une précision maximale.
Une fois ces points reportés, on les relie à l’aide d’une latte souple pour lisser soigneusement les courbes afin d’obtenir des bouchains réguliers. Les panneaux sont ensuite découpés à la scie sauteuse en plaçant la lame légèrement à l’extérieur du trait. Cet excédent “de sécurité” sera ensuite raboté à la main. Pour fabriquer le panneau jumeau, il suffit d’utiliser le premier comme gabarit. On gagnera beaucoup de temps et de précision en découpant cette seconde pièce à l’aide d’une défonceuse équipée d’une mèche à copier. Pour cela, on place le panneau-gabarit en dessous du panneau à usiner en les solidarisant provisoirement avec un adhésif double-face ou des vis.
On trace ensuite les lignes de couture le long des bords en contact puis on perce les trous de ligature à intervalle régulier, selon l’épaisseur, sur une ligne seulement. Les trous en vis-à-vis seront réalisés à la volée, au fur et à mesure du serrage. L’angle intérieur du chant du panneau doit être légèrement chanfreiné pour augmenter sa surface d’appui sur le suivant.
Il s’agit alors de tracer et découper les gabarits de montage. Comme pour une construction conventionnelle sur mannequin, il est inutile, voire nuisible, d’en multiplier le nombre. Pour obtenir une carène régulière, trois ou quatre suffisent pour une petite unité, le principe étant de laisser filer les panneaux le plus naturellement possible. Pour cette raison, les gabarits femelles et une construction à l’endroit sont nettement plus pratiques que les mâles et une construction à l’envers.
En effet, alors que les premiers sont posés librement sur une surface plane, les seconds doivent être montés et alignés en position fixe sur un châssis, une technique susceptible d’induire des irrégularités. Enfin, pour les ligatures, on peut utiliser soit du fil de cuivre, soit des colliers autoserrants en Nylon. Dans le premier cas la tension peut être réglée à la pince et le cuivre n’endommage pas les outils, mais il est cassant et peu résistant à l’allongement. Les colliers n’ont pas ces défauts, mais ils sont difficiles à desserrer et exigent des perçages de gros diamètre (3 mm ou plus).
2/ couture et congés
Fiable et durable, le cousu-collé est une technique composite bois-époxy aussi adaptée à la construction amateur que professionnelle, d’autant plus quand on l’associe à la découpe numérique des panneaux, ce qui permet de gagner encore davantage en temps de main-d’œuvre.
Une fois les panneaux et ligatures préparés (CM 229), il est temps de passer à la couture pour assembler les pièces et obtenir en quelques heures le volume définitif de la coque. Comme l’assemblage se fait en remontant de la quille vers le livet, les deux panneaux du fond sont les premiers à être posés dans – ou sur – les gabarits, eux-mêmes parfaitement alignés sur une surface plane parallèle à la flottaison. Si le bateau est de taille modeste, on peut commencer par les relier à plat, comme les feuilles d’un cahier, tout en laissant les points de ligature suffisamment lâches pour en faciliter l’ouverture.
Quand les panneaux sont posés dans les gabarits, la couture est resserrée progressivement tout le long de la ligne de quille. En règle générale, il vaut mieux commencer au milieu de la coque, autour du maître bau, et progresser ensuite alternativement vers l’étrave et la poupe. La rectitude de l’assemblage doit être contrôlée en permanence, celui-ci devant présenter une surface d’appui régulière sans désaffleur ni chevauchement.
Les panneaux sont alors immobilisés dans les gabarits, à l’aide de vis, d’un cordon de colle thermofusible, d’un adhésif double-face ou de tout autre dispositif de fixation temporaire. Puis la même procédure est reprise pour assembler les autres virures, la pose se faisant symétriquement des deux côtés pour équilibrer les tensions et éviter les déformations. La régularité des bouchains, contrôlée à l’œil, se fait en jouant sur le serrage des ligatures. Si vous utilisez du fil de cuivre, tournez vos liens toujours dans le même sens pour ne pas vous tromper…
Le moment est venu de poser les cloisons, qui doivent avoir un jeu suffisant pour ne pas poinçonner et déformer le bordé. Car c’est bien le bordé qui détermine la forme de la coque et non la structure intérieure. Si nécessaire, il faut donc rectifier le profil des cloisons, un jeu important ne posant, grâce aux collages époxy, aucun problème de solidité. La coque étant en position de flottaison, un fil à plomb et un niveau à bulle permettent d’aligner les cloisons verticalement et horizontalement. Une double mesure depuis l’étrave sert à contrôler la perpendicularité à l’axe, les gabarits pouvant aussi servir de référence pour obtenir des cotes utiles. Enfin, la pose d’un liston ou d’une bauquière – qui facilitera par la suite la pose du pont – permet de rigidifier les œuvres mortes.
Les ligatures sont supprimées après polymérisation des joints
Une fois vérifié que la coque ne présente aucun vrillage, les bouchains sont assemblés à l’aide de joints-congés époxy (CM 212), renforcés par des bandes coupées dans le biais d’un tissu monoaxial, ou mieux, dans un tissu biaxial.
Selon l’échantillonnage, plusieurs bandes de largeur croissante peuvent être superposées, en commençant par la plus étroite. L’architecte définit le rayon et la matière des congés, à haute ou basse densité, en fonction des efforts à supporter et de l’épaisseur du contre-plaqué. La méthode empirique veut que l’épaisseur d’un congé haute densité reste à peu près égale à celle du contre-plaqué, avec une largeur correspondant à quatre fois son épaisseur environ, cette estimation étant à doubler pour un congé basse densité.
Pour éviter de déformer le contre-plaqué en marchant sur le bordé, il vaut mieux en général travailler depuis l’extérieur de la coque ou depuis des passerelles suspendues à l’intérieur.
Les ligatures, qui n’ont plus aucun rôle après la polymérisation, sont arasées, ou mieux, retirées pour préparer la coque à la stratification (CM 215), le contre-plaqué restant sensible au poinçonnement local. Si vous avez “chenillé” les bouchains – sur une petite unité, il est très commode de poser ainsi des points de colle époxy entre chaque ligature –, vous pouvez d’ailleurs enlever les ligatures avant de poser les joints-congés définitifs. Sur les unités plus importantes, dont les coutures sont noyées dans la résine, on peut se contenter d’araser au ciseau à bois les colliers en plastique ou les fils de cuivre dont la matière est suffisamment tendre pour ne pas abîmer le tranchant de l’outil.
Avec des ligatures en fil de fer, employées sur les plus gros bateaux, il suffit de défaire la boucle et de la chauffer en appliquant quelques secondes un courant basse tension à forte intensité, en provenance d’une batterie ou d’un poste de soudure électrique. La chaleur fait fondre la résine le long du fil et facilite son extraction à la pince.
Plus proche des techniques composites que de celles du bois conventionnel, la construction en cousu-collé permet de limiter l’usage du bois massif aux pièces non-structurelles ou à la décoration, au profit de renforts stratifiés, plus légers et plus faciles à mettre en place. Rien n’empêche par exemple de combiner une coque en contre-plaqué avec un pont en sandwich, qui allégera les hauts et protégera mieux les emménagements de la chaleur solaire. Les appendices, quille, aileron, etc. sont posés de manière conventionnelle par collage ou par boulonnage. Restent alors les finitions, simples à réaliser à condition d’éviter les couleurs foncées qui favorisent le marquage des tissus à travers la peinture après quelques semaines d’exposition au soleil, tout en augmentant la température intérieure.
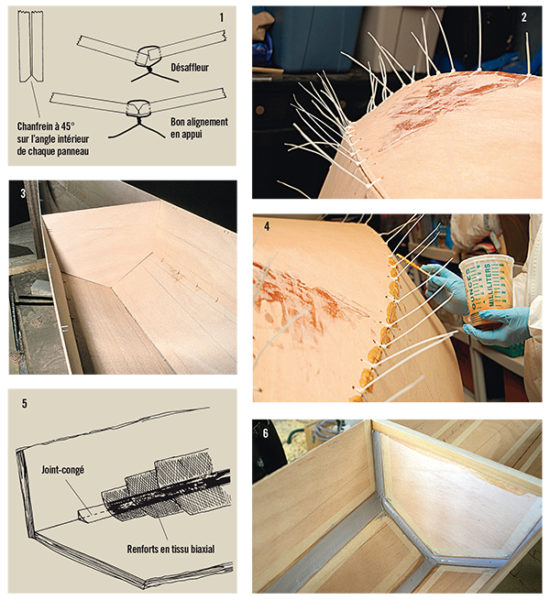
2) En raison d’une erreur de développé, le bouchain présente ici une inversion sensible de sa courbure, ni esthétique
ni favorable aux écoulements.
3) Les cloisons doivent s’insérer dans la coque avec un jeu suffisant pour ne pas déformer le bordé.
4) Le chenillage de points de colle entre les ligatures permet de les retirer plus facilement qu’une fois noyées
dans la résine des joints-congés.
5) Les bouchains sont assemblés à l’aide de joints-congés époxy renforcés par des bandes de tissu.
6) Avant de poser un joint-congé dans chaque angle de la structure, il faut s’assurer que la carène ne présente aucune déformation.