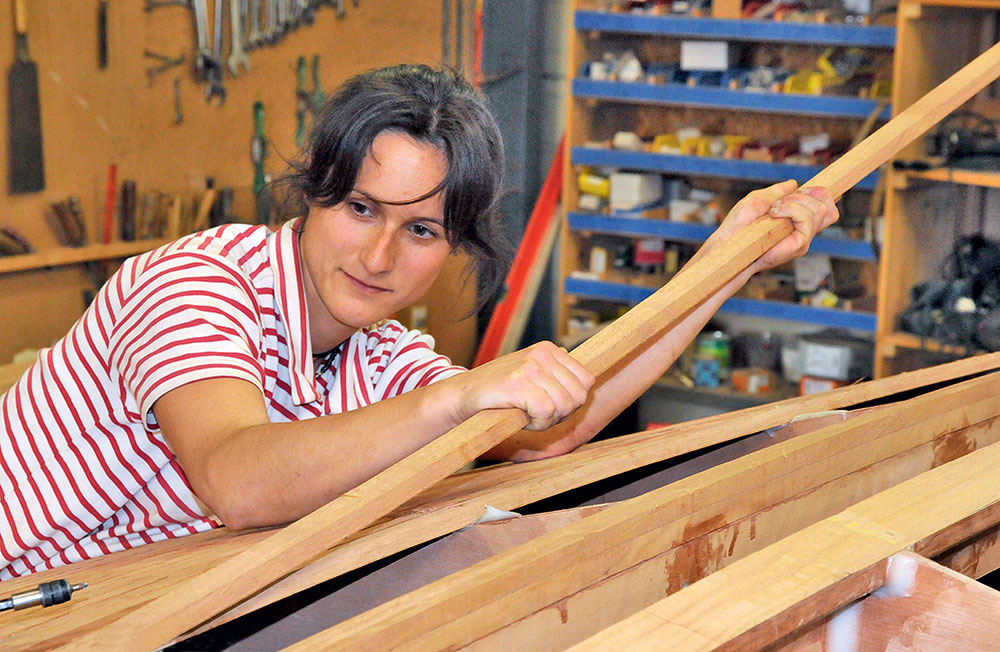
Le bordé latté
Avant la pose
Parfois appelé «strip planking», le bordé latté est l’une des techniques les plus polyvalentes qui soient pour construire une coque en formes, à l’unité ou en petite série. Ses performances mécaniques sont de haut niveau, pour un prix et un temps de mise en oeuvre raisonnables.
Le principe du bordé latté n’est guère différent de celui du traditionnel bordé franc. Les bordages, dont les jonctions se font bord à bord, sont divisés et orientés longitudinalement; l’ensemble est relié par une structure transversale (membrures et cloisons). Les virures ont toutefois une largeur beaucoup plus faible, ce qui permet de se passer du brochetage et du calfatage.
L’assemblage des lattes profite désormais de la qualité des collages à l’époxy, beaucoup plus fiables et homogènes que le clouage sur chant originel, qui imposait des lattes assez épaisses (15 mm ou plus) pour éviter que le bois n’éclate ou que les clous ne ressortent du bordé. Afin d’assurer une étanchéité correcte, il fallait alors ajuster les faces en contact et équerrer les lattes à la volée sur toute leur longueur. En cas de réparation, le clouage, très serré et décalé d’une latte à l’autre, compliquait sérieusement le travail.
L’assemblage collé est stable, parfaitement étanche et, surtout, bien plus rapide à exécuter. Légères et faciles à manipuler, les lattes peuvent être usinées dans de nombreux bois, même s’il est préférable de privilégier les essences les plus stables, au fil droit, sans nœuds ni contre-fil trop marqué. Dans le cas d’un bordé composite, elles doivent en outre être les plus légères possible. Très esthétique une fois verni, le red cedar fait partie des classiques, mais certains bois européens ou africains sont tout aussi adaptés, comme l’épicéa ou les acajous légers de type Grand Bassam, Agba, Samba, etc.
Polyvalente par nature, la mise en oeuvre du bordé latté repose sur l’existence de gabarits plus ou moins nombreux, mâles ou femelles, temporaires ou définitifs. Il y a quelque temps, on combinait
le lattage à des plis extérieurs en bois moulé. Les lattes, épaisses, servaient alors de support rigide pour poser les plis de bois tranché, ce qui permettait en outre de réduire la structure interne et la quantité de bois tranché à poser. Mais cette synthèse impose de maîtriser simultanément les deux techniques, et de cumuler le coût de leurs matériaux respectifs. Aujourd’hui, la solution la plus courante passe par un lattage renforcé par une stratification sur une ou deux faces; cette dernière méthode s’apparente à une structure en sandwich où le lattage formerait l’âme, renforcée par des peaux en fibres synthétiques ou naturelles.
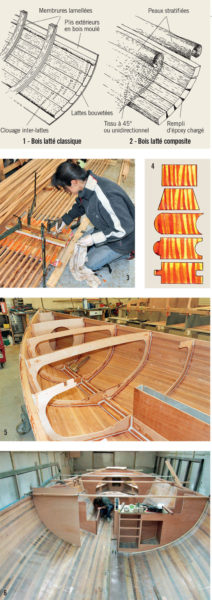
et le bois moulé.
2) La solution le plus courante
aujourd’hui consiste à renforcer
le lattage par une stratification.
3) Un assemblage par scarf permet d’obtenir des lattes de n’importe quelle longueur, indépendamment de celle des débits.
4) Si une latte rectangulaire convient bien pour les zones tendues du bordé, des profils à encastrement peuvent être utiles pour les zones à fortes contraintes.
5) Dans la construction lattée,
la structure transversale
a une importance particulière, surtout en l’absence, comme ici,
d’une stratification intérieure.
6) Sur cette coque en construction
d’un voilier de croisière de 9,50 mètres, la stratification des lattes est continue, sans coupure
des tissus de l’étrave au tableau. Les cloisons sont rapportées par-dessus.
Cette conception spécifique nécessite néanmoins le respect de certaines règles. Le lattage n’ayant qu’une faible cohésion transversale dans la mesure où les fibres du bois sont quasi exclusivement orientées dans la longueur, la structure transversale devra avoir un maillage suffisant pour résister aux sollicitations les plus fortes. L’architecte devra par ailleurs veiller à la bonne répartition des efforts sur le bordé en intégrant les éléments de renfort (quille, puits de dérive, varangues, etc.) à l’ensemble, de préférence sans fixations mécaniques. Les peaux stratifiées devront en outre avoir un échantillonnage identique sur chacune des deux faces afin que le bordé soit mieux équilibré, et la stratification intérieure sera autant que possible continue, c’est-à-dire sans interruption au droit des cloisons ou des éléments de renfort.
CHOISIR ET FABRIQUER SES LATTES
La section des lattes – qui peuvent être scarfées (CM 214) pour obtenir les longueurs nécessaires à la construction – répond à des contraintes de forme, au choix du mode d’assemblage et, surtout, à l’orientation du fil. Si des lattes carrées peuvent être orientées de manière optimale sans avoir à se préoccuper du fil des débits, leur coût et le temps de travail qu’elles imposent, notamment au maîtrebau, deviendront vite prohibitifs, quelle que soit leur épaisseur (de 6 à 25 mm selon la taille du bateau). Les lattes de section rectangulaire, au rapport largeur/épaisseur de 1 à 3 en moyenne, sont plus commodes, d’autant qu’il est tout à fait possible d’en faire varier la largeur en fonction des formes de la carène.
Ainsi, des lattes plus larges peuvent couvrir rapidement la partie haute du bordé, là où la courbure est généralement tendue, tandis que d’autres, plus étroites, seront utilisées lorsque le vrillage est important, comme dans les zones du brion ou du retour de galbord. À ces endroits de fortes contraintes, les lattes tendent en effet à sortir du plan et à se désaligner. Pour limiter ce défaut, on peut réduire l’espacement des gabarits ou utiliser des lattes dotées d’un profil à encastrement (convexeconcave, moulure mâle/femelle, rainure/languette, etc.). Ces profils plus complexes, qui possèdent une certaine capacité d’autoalignement, induisent néanmoins deux toupillages supplémentaires pour leur fabrication. Ils nécessitent aussi de prendre en compte une perte de matière, d’autant plus importante que la section est faible: on imagine mal un système rainure/languette sur une latte de 6 mm d’épaisseur! Pour calculer vos débits, il faut donc tenir compte des pertes de sciage, jusqu’à 50 % ou plus sur les faibles sections. Comptez également 10 % de lattes surnuméraires pour compenser d’éventuels défauts (gerces, noeuds, contre-fil, etc.).
Enfin, pour obtenir un bordé d’épaisseur constante et éviter les désaffleurs, dont l’élimination exige un pénible travail de ponçage ou de ragréage, il vaut mieux raboter au moins une face, celle qui sera tournée vers l’intérieur. La pose, peut alors commencer.
Le moule et la répartition des lattes
Une fois le type de latte, choisi et usiné, il est temps de réaliser le moule. Couples permanents ou gabarits temporaires, mâles ou femelles, là encore, la liberté est grande pour trouver la solution la mieux adaptée à votre projet.
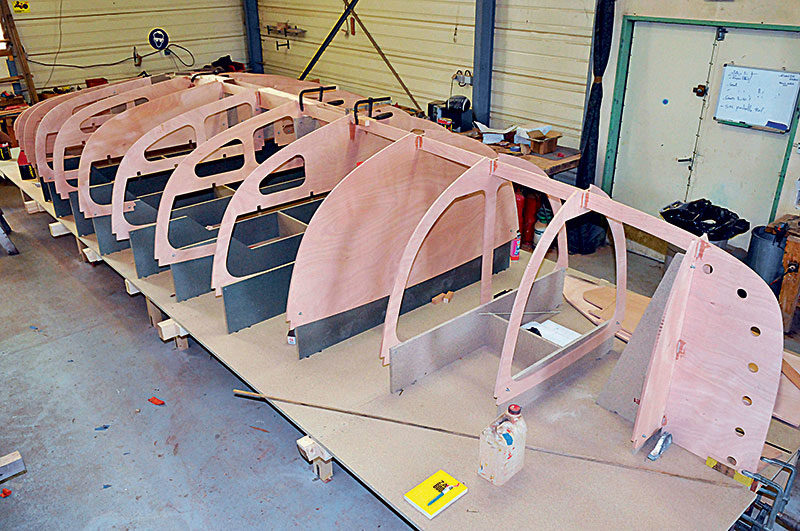
Par rapport au moule d’une coque en stratifié, laquelle exige une surface continue, celui utilisé pour un bordé latté est largement simplifié puisqu’il ne comprend que des sections transversales régulièrement réparties sur la longueur de la coque. Ces sections peuvent être découpées manuellement dans un panneau de contre-plaqué ou d’aggloméré, ce dernier étant moins cher mais aussi moins stable et peu apte à la tenue des vis ou des agrafes. Pour une bonne accroche de ces dernières, et pour que les gabarits ne se déforment pas au moment de la pose des lattes – qui peuvent induire des efforts importants –, les panneaux doivent faire au minimum 10 mm d’épaisseur. L’ensemble du chantier peut en outre être rigidifié avec des entretoises ou des étais temporaires fixés à l’aide de vis autotaraudeuses.
Un usinage numérique (CM 192) permet d’obtenir des sections d’une précision incomparable sans avoir à exécuter le moindre tracé en grandeur. Les gabarits peuvent être soit temporaires, soit intégrés à la structure du bateau conjointement à d’autres éléments (varangues, carlingues ou équipets), soit mixtes. L’espacement – ou “pas” – des gabarits varie en fonction de la raideur des lattes que déterminent leur épaisseur et la densité de l’essence utilisée. En règle générale, on peut compter sur trente à soixante-dix fois l’épaisseur nominale – soit, par exemple, de 270 à 650 mm pour une latte de 9 mm –, sachant que plus l’espacement est grand et la latte mince, plus elle tend à faire des plats et à retrouver la ligne droite entre chaque appui. Pour éviter toute déformation, des couples supplémentaires peuvent être nécessaires dans les zones à forte sollicitation comme le brion et le retour de galbord, ou lorsque le frégatageou le tulipage sont prononcés.
Sur les grandes unités, le moule intègre les pièces de quille et d’étrave, souvent lamellées en place, ainsi que les bauquières et le tableau. Sur les bateaux plus petits, ces éléments peuvent être fabriqués séparément puis rapportés, leurs faibles taille et poids rendant les manutentions plus aisées.
Le moule est traditionnellement mâle, quille en l’air, mais on peut aussi construire à l’endroit dans des gabarits femelles. Cette solution est particulièrement intéressante dans le cas d’une structure en sandwich pour stratifier la peau intérieure du bordé sans interrompre la continuité des fibres de renfort par des éléments de structure. Les lattes suivent très précisément les formes de la carène, le tracé des gabarits n’exigeant aucun calcul de déduction de bordé. Un moule femelle permet également de construire la quasi totalité du bateau – y compris les cloisons, les emménagements et le pont – à l’intérieur des gabarits, ceux-ci servant de référence pour les mesures et le positionnement de la structure.
LES QUATRE SCHEMAS POSSIBLES DE LATTAGE
Les lattes ayant une largeur constante – elles ne sont pas brochetées –, elles sont ployées et ajustées sur l’axe au fur et à mesure de la pose. Or, compte tenu des formes de la plupart des carènes, le développé transversal du bordé est plus important au maître-couple qu’au tableau et à l’étrave… Quatre schémas de mise en oeuvre des lattes existent: la pose peut être parallèle au livet, parallèle à la quille, mixte, ou parallèle à une latte-maîtresse. La technique retenue dépend du type de lattes et de la finition, vernie ou peinte.
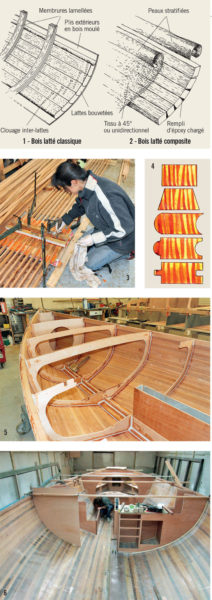
permet de respecter les cotes exactes de la carène et de construire la quasi totalité
du bateau à l’endroit.
2) Un moule femelle en deux parties – ici celui d’une yole de mer en red cedar – permet d’accéder confortablement à l’intégralité du bordé.
3) Les différentes possibilités de mise en oeuvre des lattes: parallèles à une latte maîtresse (A), parallèles au livet (B),
mixte (C), parallèles à la quille (D).
4) Avec un lattage parallèle au livet, la courbure des lattes s’accentue à la quille, où elles doivent être ajustées en biseau.
Le lattage depuis le livet est le plus facile au départ, mais la courbure s’accentuant vers la quille, les lattes doivent y être ajustées en biseau. Cette solution, qui supporte mal les concavités d’un tulipage ou d’un retour de galbord prononcés, convient pour une carène plutôt pleine, à convexité constante et d’un rapport bau/longueur assez réduit. À l’inverse du précédent, le lattage depuis la quille est rarement esthétique avec un bordé verni car les coupes biaisées des lattes se retrouvent le long du livet, donnant l’impression qu’elles “sortent” de la coque.
La méthode mixte, la plus polyvalente, consiste à poser les lattes à la fois depuis la quille et le livet, ce qui permet de diviser le bordé en deux zones. Cette solution convient bien pour une finition vernie. Enfin, la dernière technique, bien adaptée aux formes complexes, consiste à faire filer une latte, placée en position médiane au niveau du maître-couple, le plus naturellement possible vers
les extrémités. Le reste du bordé est ensuite posé de part et d’autre de cette référence, alternativement vers la quille et le livet.
Quel que soit le schéma de lattage retenu, il est impératif de border les deux côtés en même temps, en n’arrêtant les opérations qu’après avoir posé un nombre égal de lattes à tribord comme à bâbord. Cette précaution permet d’équilibrer les contraintes exercées sur le moule et de limiter les risques de déformation. Dans presque tous les cas, la zone problématique se situe autour du brion, ce qui conduit certains constructeurs à interrompre le lattage sur un couple situé en arrière de l’étrave et à tailler le volume restant dans un bloc en bois lamellé ou en mousse stratifiée. Cette pièce qui pourra faire office de “crash box” d’abordage, peut également faire l’objet d’un usinage numérique en trois dimensions.
Collage et stratification
Si les lattes peuvent être posées à sec avant de charger les joints, il est également possible de les solidariser au fur et à mesure du montage. Le collage puis la stratification du tissu de renfort sont destinés à apporter à la structure la cohésion et la résistance finale qui lui manquent.
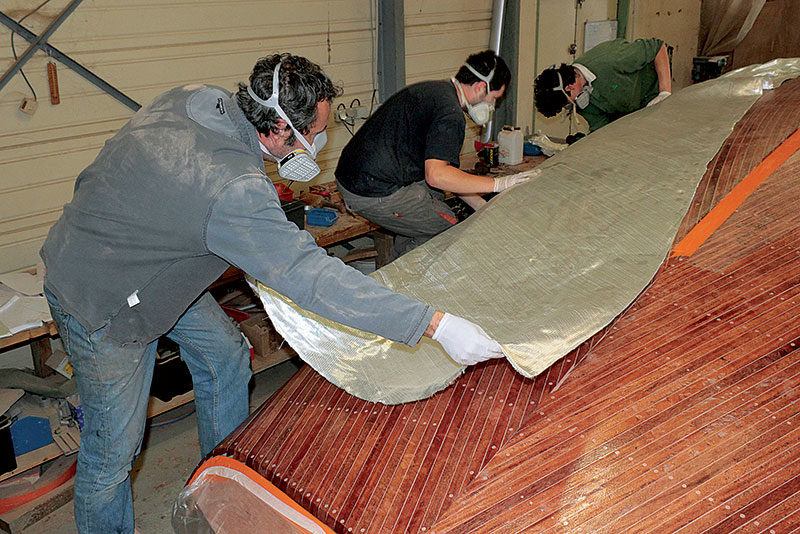
La technique de pose dite “humide” consiste à encoller le chant des lattes et à les visser sur les gabarits au fur et à mesure du montage. Souvent prônée par ceux qui ne l’ont jamais mise en oeuvre, cette méthode reste fastidieuse pour le constructeur. Mais c’est la seule possible lorsqu’on utilise des profils de latte à encastrement . Chaque joint ne représentant qu’un faible volume, l’opérateur ne peut préparer qu’une petite quantité de mélange (résine, durcisseur et charge) à la fois, qu’il doit étaler de manière homogène sur toute la longueur de la latte avant de poser la suivante. Même en travaillant proprement, ce procédé est extrêmement salissant, l’époxy finissant immanquablement par se déposer à peu près partout sur l’outillage et le chantier. La préparation de la colle par très petites quantités engendre par ailleurs des pertes importantes de matière… et l’époxy reste un produit coûteux! La pose humide exige aussi une excellente planification des différentes opérations: préparation de l’adhésif, dépose du cordon de colle, pose de la latte sur les gabarits, agrafage ou vissage, puis raclage des excédents à l’intérieur comme à l’extérieur du bordé avant durcissement. Les tâches à exécuter en continu étant nombreuses, il est donc difficile de travailler seul.
La solution consistant à séparer la pose du collage sera préférée pour tous les autres types de lattes. Le remplissage des joints s’effectue par ratissage du mélange adhésif déposé à la spatule sur le bordé, ou par injection sous pression à l’aide d’un pistolet pneumatique ou d’un adhésif en cartouche. Un seul opérateur peut ainsi couvrir de grandes surfaces, proprement et à son rythme, en déposant des quantités substantielles de colle, sans aucun risque de polymérisation prématurée ou d’exothermie. La méthode sèche impose toutefois d’avoir des joints larges, ce qui implique un volume de colle plus important que pour la pose humide; mais, comme les pertes sont quasi nulles, la consommation de colle reste équivalente.
Bien qu’ils puissent être colorés, les joints épais peuvent perturber l’esthétique d’une finition vernie. En travaillant avec des gabarits femelles, on peut les placer du côté intérieur du bordé, où ils seront bien moins visibles. Pour éviter de créer des bosses au ponçage, la densité de l’adhésif doit être proche de celle de l’essence de bois utilisée. On recourt pour la réguler à des charges légères, microballons phénoliques ou microsphères de verre. Si l’on souhaite que la coque soit vernie, donc sans enduit, le ponçage final doit être soigné, d’abord à l’archet dans le sens du fil, puis à la ponceuse orbitale avec un grain fin (120 et 240). Certaines essences de faible densité comme le red cedar sont en effet sensibles aux rayures en travers du fil, lesquelles se traduisent, après imprégnation, par des traits foncés visibles sur un fond plus clair. Une finition peinte se contentera d’un ponçage moins poussé, au grain 80 par exemple.
DES TISSUS POUR PROTEGER OU RENFORCER
La conception structurelle du bordé latté varie selon les architectes et les constructeurs. Certains privilégient une forte charpente avec des lattes épaisses (25 mm ou plus) réalisées dans des essences semi-dures et collées sur chant (en lieu et place des clous traditionnels). En ce cas, le tissu extérieur n’a qu’un rôle structurel secondaire et la stratification ne sert qu’à protéger les lattes contre le poinçonnement, une simple imprégnation époxy permettant d’étancher l’intérieur. La construction reste donc proche de celle d’une unité en bois classique, avec l’inconvénient d’un devis de poids important.
D’autres constructions s’inspirent au contraire des sandwiches composites à haute performance, avec une âme lattée en bois léger (red cedar, samba, épicéa…) assez mince (de 10 à 25 mm) en lieu et place de la mousse PVC. On y ajoute deux peaux stratifiées, équilibrées sur chaque face avec un ou plusieurs plis de tissu de renfort. Cela donne une très grande rigidité au bordé, qui voit ainsi sa charpente intérieure s’alléger. D’autant que les emménagements sont le plus souvent rapportés sur le bordé à l’aide de joints-congés afin de maintenir la continuité de la peau intérieure; comme dans la construction composite, ils ont un double rôle, fonctionnel et structurel. Bien étudiée, cette solution permet de gagner un poids et un temps de main d’œuvre importants.
En général, les tissus utilisés pour la protection sont plutôt légers (de 160 à 300 g/m2), avec une armure de type sergé qui s’adapte à toutes les formes de carène et reste parfaitement transparente sous un vernis. Pour le renfort, les tissus sont, sauf sur les petites unités, plus lourds (300 g/m2 et plus), avec une armure bi ou triaxiale qui augmente la résistance en torsion du bordé. En revanche, l’opacité naturelle de ces tissus est incompatible avec une finition vernie. Après polymérisation, on égrène la surface manuellement puis on enduit au couteau ou au rouleau selon le type de produit. La coque est lissée à l’archet et débarrassée de ses éventuels défauts, travail fastidieux et physiquement éprouvant, mais indispensable pour obtenir une finition de qualité.
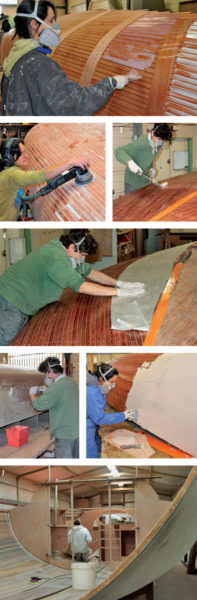
Une fois le bordé recouvert d’une couche de résine pure (3), le tissu peut-être posé (4). L’imprégnation s’effectue
au rouleau (5) jusqu’à obtenir une surface transparente dépourvue de traces sèches et blanches. Après égrenage, l’application d’un enduit – ou de trois couches de résine pure pour une finition vernie –
permet de ragréer la surface (6)
afin d’éliminer les principaux défauts. Un bordé stratifié sur chaque face (7) forme une structure en sandwich
légère et très rigide.