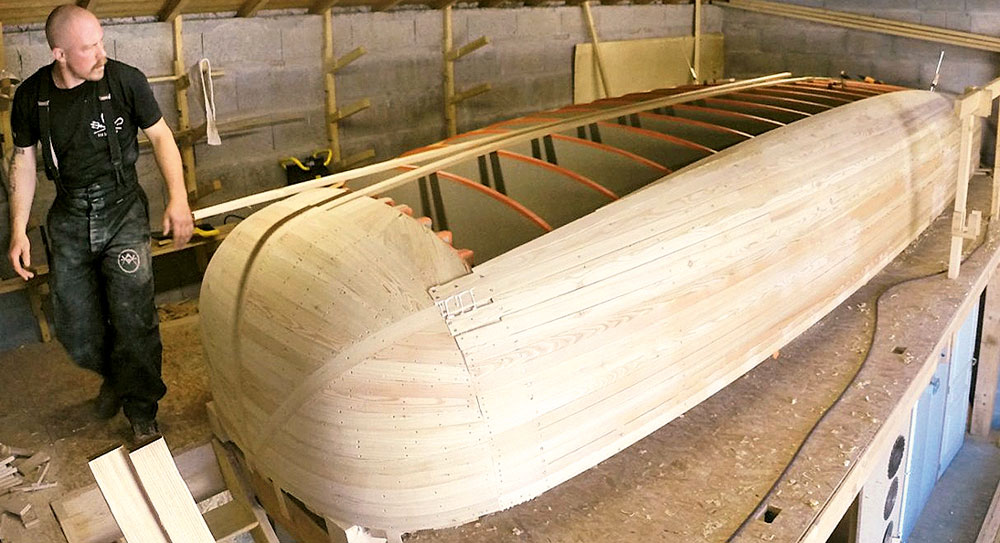
À Saint-Léger-les-Vignes, en Loire-Atlantique, Flavien Gaulard construit actuellement un voilier de 5,50 m original et très enthousiasmant, comme d’ailleurs et plus largement son projet… « J’ai créé mon chantier, Kaori, il y a un peu plus d’un an, précise-t-il. Auparavant, j’avais travaillé dix ans comme charpentier dans le bâtiment, en France, avant une expérience de cinq ans aux Philippines, dans le secteur naval et maritime. »
Depuis son retour en France, Flavien a renoué avec le bâtiment, mais il souhaitait également se lancer dans la construction navale, conscient que « pour espérer vendre un bateau, il faut d’abord le construire pour montrer son savoir-faire. » C’est ainsi qu’il a sollicité l’architecte naval Gildas Plessis. « Je lui ai exposé mes deux contraintes principales, précise-t-il, à savoir la longueur de mon atelier (7,10 m) mais surtout le fait que ce bateau devait être conçu afin d’être le plus “propre” possible, de la conception à la navigation. »
Gildas Plessis s’oriente d’emblée vers un scow, un type de carène qu’il connaît très bien. « Au cahier des charges de Flavien, j’ai ajouté “joli” et “rapide”, comme les Nord-Américains savaient le faire sur ces bateaux il y a plus d’un siècle. Et c’est ainsi que le programme s’est bientôt résumé à une question : comment faire un bateau contemporain, à l’esthétique identifiable, en minimisant autant que possible les produits néfastes à l’environnement entrant dans sa construction ? »
La coque du Kaori 5,50 – c’est son nom – va faire appel à du « bois d’arbre », massif. « Il fallait qu’elle soit légère, précise Flavien, et, pour optimiser le bilan carbone, il fallait une essence locale. C’est ainsi qu’on a retenu le mélèze pour un bordé assez épais, 18 mm, afin de limiter la quantité de résine mise en œuvre. » Flavien a façonné lui-même les cent quatre-vingts lattes de 4 m de long, aux chants bouvetés. Le bordé terminé, il le recouvre à l’extérieur de trois couches de sergé de lin de 400 g/m2 avec une résine époxy Sicomin bio-sourcée à 35 pour cent.
« À ce stade du projet, poursuit Flavien, cette résine et l’usage d’acétone sont un des compromis à notre quête du “propre”. La structure en contreplaqué okoumé en est un autre. Faute de temps, nous avons choisi ces panneaux en bois africain, découpés par Naviline. Le second exemplaire, sera construit avec un contreplaqué local et performant que nous étudions. » Le rouf de ce prototype sera lui aussi un compromis. Sa forme empêchant le ployage des lattes, il sera réalisé en mousse polyéthylène (PE). « Ce matériau est issu du recyclage de bouteilles d’eau, précise Flavien. D’ailleurs, c’est également du PE que je compte utiliser sur la prochaine unité afin de façonner l’étrave comme une crash-box, celle de ce numéro 1, en bois moulé, ayant été trop complexe à réaliser. »
Flavien ne s’est pas arrêté à ces considérations sur les matériaux durant la construction. Les déchets sont soigneusement comptabilisés. « Pour l’heure, la construction en a produit un seul grand sac-poubelle, essentiellement rempli… d’emballages ! Quant aux copeaux et sciures, je les récupère pour les mettre à la disposition d’utilisateurs de toilettes sèches. Au pied du chantier où je travaillais aux Philippines, on aurait pu ramasser chaque jour l’équivalent d’un camion poubelle de déchets… Ça ne s’oublie pas. »
En plus de sa stabilité de forme, la carène de scow du Kaori 5,50 permet de l’emménager avec un grand cockpit ainsi qu’un grand couchage à l’avant. La mise à l’eau de ce day-boat à dérive est prévue à l’automne.